There are plenty of reasons why you should organise warehouse inventory properly from the outset. As well as supporting inventory control and time management, it streamlines your operations for unparalleled productivity.
That said, arranging warehouse inventory is no small feat if you don’t know where to start. Which warehouse layout works best? What type of shelving should you use? How should you categorise inventory?
In this simple guide, we explain how to organise inventory in a warehouse for long-term success, from receiving orders and labelling stock to cleaning every corner and performing audits. Plus, discover the benefits of an orderly space for your business.
Keep reading to learn how to manage warehouse inventory, minimise errors and maximise efficiency.
Benefits of warehouse inventory control
Here’s why it pays to organise inventory in a warehouse wisely.
Faster processing
One of the main advantages of investing in warehouse organisation is to save your staff valuable time. With a solid warehouse inventory management system, workers know exactly where each item is stored. That means less wandering around searching for products and, ultimately, quicker order fulfilment.
Higher productivity
It’s easy to lose track of items, make mistakes and waste valuable resources in a cluttered and chaotic warehouse. Therefore, logical warehouse inventory planning can drive productivity. With a standardised system in place, employees are equipped to get the job done more effectively.
Extra storage space
By tidying up your warehouse’s inventory, you’ll free up more room for other items. And it’s usually less expensive to arrange your inventory by re-structuring your current warehouse systems than it is to buy or rent an additional storage facility.
Improved safety
Given the kinds of equipment and machinery found in a warehouse, worker safety is of paramount importance. And a disorganised space brings more potential hazards. Storing inventory in an orderly way within designated areas will help to keep your warehouse clutter-free, in turn reducing the risk of injuries on the floor.
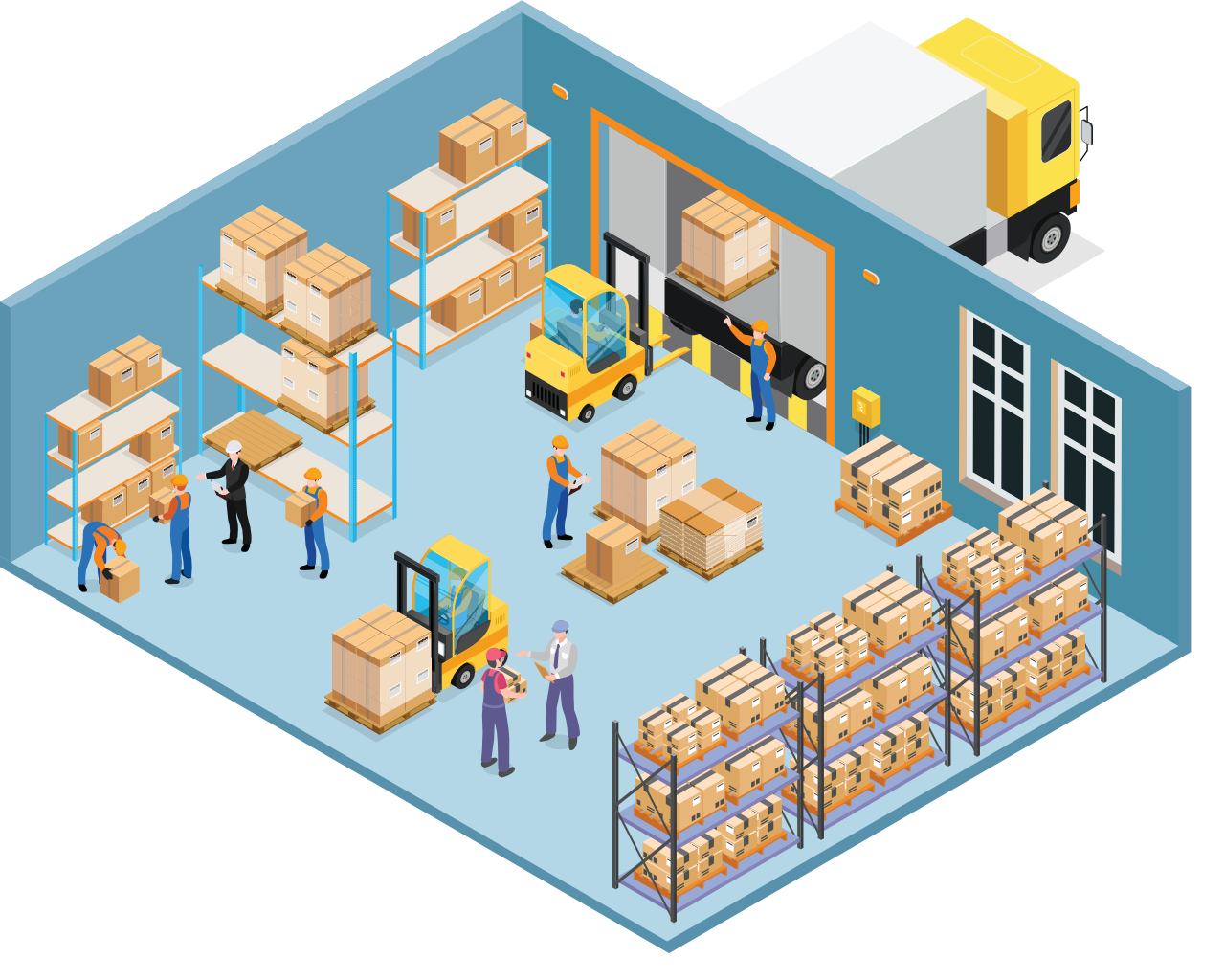
How to organise warehouse inventory in 10 steps
Follow these easy tips on how to organise inventory in a warehouse effectively.
1. Create a seamless floor plan
Whether you’re starting from a blank slate or ready to update an existing layout, the right floor plan should flow in the order of operations.
Your inventory should move through the steps, from receiving and storage through to packaging and dispatch in a streamlined sequence.
To ensure this, design your warehouse’s floor plan on paper or using online software and then draw a line symbolising the flow of your inventory’s journey through it. Where is it received? How is it handled? Where does it leave? Ideally, this line should be practically straight.
During this process, discuss the potential new design with your staff to see if there are any areas of your warehouse that could be tweaked to support inventory management.
2. Assign a designated receiving area
On a related note, make sure there is a designed area for receiving incoming deliveries. This area is usually at the back of your warehouse, with the front being reserved for dispatch and client service.
Estimate the average quantity of deliveries to work out the required space. There should be enough room to sort arriving items before transporting them to the relevant section of your warehouse.
3. Arrange inventory with ABC analysis
Organise your warehouse using the ABC Analysis, which involves sorting stock into three distinct categories:
A items: Your best-selling, fast-moving items make up approximately 80% of orders or 20% of stock. Store them in the most accessible place, nearest to customers or the shipping bay, which is typically towards the front of your warehouse.
B items: Mid-range items sell often and tend to account for about 15% of orders or 30% of stock. They should be stored in the second most convenient section.
C items: Slow-moving items account for 5% of orders or 50% of stock. You can store this inventory towards the back of your warehouse, as it is processed less frequently than the rest.
Importantly, if you deal with items that have an expiration date, store fresh stock behind older stock so that products are dispatched in a way that minimises waste.
4. Choose storage solutions carefully
Select shelving and storage solutions that suit your physical space and operational requirements. When considering warehouse storage systems to arrange your items, remember to make use of vertical space, prioritise safety and support a smooth traffic flow.
Pallet racking systems are favoured for their durability, safety and strength, all while making the most of vertical space. Servicing as the base for your warehouse organisation, there are many different types to consider, such as:
- Selective racking;
- Longspan shelving;
- Medium-duty cantilever racks; and
- Heavy-duty cantilever racks.
At Pallet Racking Sydney, we have them all. The right choice for your warehouse racks depends on the type of operations underway, as well as the size and quantity of items you need to store. Our team is always happy to help you weigh up your options.
5. Label, label, label
Labelling your inventory and locations helps to keep your warehouse and workflow organised.
Firstly, your team won’t have to open and root around in a storage container to discover its contents. Instead, they’ll know precisely what’s inside with one look at the label. As a result, your warehouse will be simple to navigate, and its items easy to pick and pack.
Additionally, every SKU should be clearly marked upon product receipt for instant identification. While a sticker details the name of a product, the SKU label is a unique string of letters and numbers. Workers scan this code to correspond with your digital inventory, giving you an accurate record of stock levels. For total ease, store each SKU on its own shelf.
Next, title inventory areas based on the items they store. For instance, if you’re a frozen food supplier, your warehouse storage sections could have names like “vegetable zone” and “meat zone”. This will create a clear warehouse layout for quick and easy sourcing.
6. Colour code different sections
Another option is to colour code various areas of your warehouse according to inventory type. This helps workers to identify the general vicinity of items in a single glance.
For instance, you could use green racks for storing best-selling items, blue racks for mid-range items, and red racks for slow-moving items.
7. Take advantage of technology
Utilise inventory management software to keep track of your warehouse’s items. Although going paperless might seem daunting at first, this worthwhile investment will make record-keeping easier and more cost-effective in the long run.
With a suitable online inventory management system, you’ll be able to automate stock control, order fulfilment, and supply chain procedures. This game-changing technology can note sales, monitor inventory levels, track shipments, and more in real time.
8. Manage all wires
Take steps to keep warehouse wires protected, tidy and out of the way of your operations. To do this, use accessories such as cable protectors, covers, cord clips, and ramps.
Cable identification tags and ties will also help your team to know which wire can be unplugged if needed.
9. Keep your warehouse spick and span
Regular maintenance and tidying are important when it comes to how to organise inventory in a warehouse. This is because items are inevitably moved and sometimes misplaced during day-to-day operations.
So, establish a routine warehouse cleaning system on a daily, weekly or monthly basis to tidy up materials, stock, equipment and more. As well as ensuring aisles remain clear of any obstacles, this process will help you to accurately account for inventory and create a calm, orderly work environment.
10. Perform audits and reviews
Last but not least, carry out periodic assessments of your inventory management and organisation systems. This process should take a look at everything from inventory categorisation and storage to workflow and cleaning schedules.
See if there is any room for improvement when it comes to maximising space, optimising inventory handling, and removing barriers to productivity. Above all, you’ll need to ensure that your warehouse inventory setup meets all safety standards.
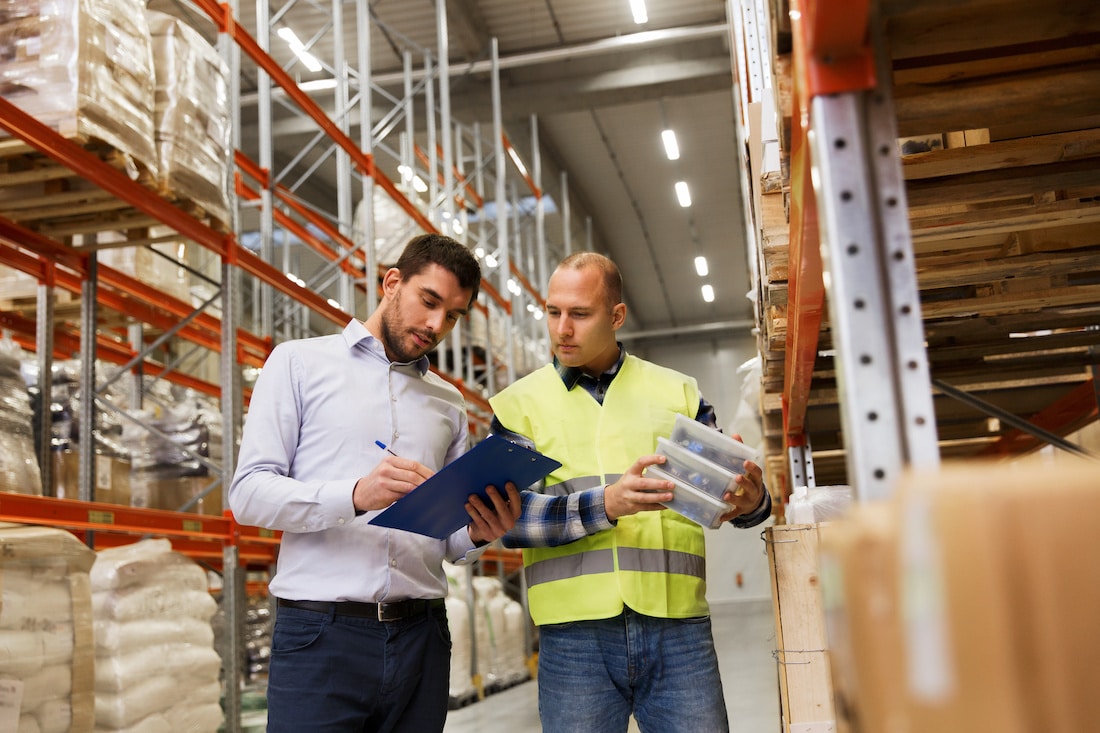
Optimise warehouse inventory storage with Pallet Racking Sydney
A neat, streamlined warehouse enables you to improve efficiencies, reduce errors and ultimately get the most out of your business. And now that you know how to organise inventory in a warehouse, it’s time to equip your team with the right solutions.
Optimise inventory storage with premium-quality pallet racking systems. At Pallet Racking Sydney, we provide affordable, durable and tailored storage solutions for any facility. Our range includes Schaefer selective racking, cantilever racking, longspan shelving and racking accessories.
Shop online or contact Pallet Racking Sydney today.